Packaging
SuperPE project: a new innovation to make recycled PE and PP plastics suitable for contact with foodstuffs
10
Jul
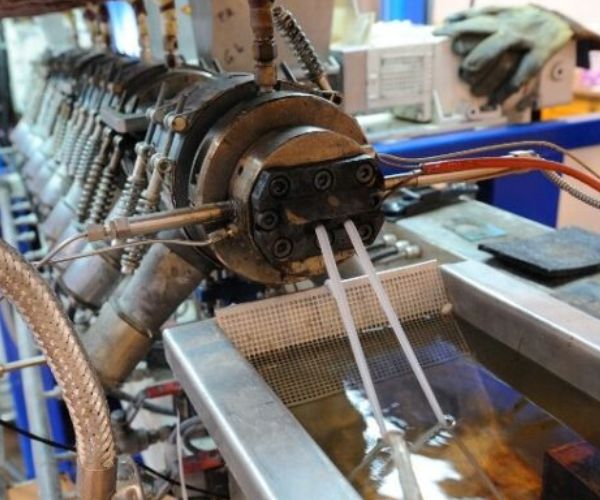
Published on: 10/07/2023
PE and PP alone account for over 50% of the plastics used in packaging.[1] (e.g. butter trays, milk bottles, water packaging film, cosmetic jars and tubes, etc.). Being able to guarantee the sanitary safety of mechanically recycled materials intended for contact with foodstuffs to both manufacturers and the relevant authorities is a key challenge for the recycling and plastics industries, and a major innovation for these materials.
The SuperPE consortium brings together 6 players in the packaging or supercritical CO2 treatment sector, bringing analytical, technological and industrial expertise to the project, winner of the Eco-design, recycling and recovery call for projects led by Citeo in 2019.
Over 99% decontamination
The SuperPE consortium has defined operating conditions for decontamination using supercritical CO2. The results obtained are more than encouraging, since it has been shown that it is possible to decontaminate low molar mass compounds (of the order of 300 g/mol) in excess of 99%. For higher molar mass compounds, yields of the order of 90% were achieved. These results were first established on model compounds, selected on the basis of analyses of post-consumer recycled materials from household waste. They were then confirmed directly on the decontamination of these same commercial recycled materials. Treatments were carried out up to pre-industrial scale, processing batches of 80 liters of material. Finally, economic modeling of the SuperPE process demonstrated the viability of an initial industrial-scale tool.
SuperPE paves the way for an industrial process that enables post-consumer PP and PE recycled materials to be chemically decontaminated at a level of performance compatible with the requirements set for food and cosmetics packaging.
[1] PlasticsEurope, The Facts 2022
Press contacts
Citeo - Marion Fajgenbaum / Megane Breton
presse@citeo.com
06.34.55.38.73 / 07.52.60.62.30
About :
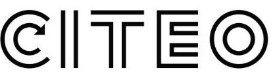
Citeo is a company with a mission created by companies in the consumer goods and distribution sectors to reduce the environmental impact of their packaging and paper, by offering them solutions for reduction, reuse, sorting and recycling. To respond to the ecological emergency and accelerate the transition to a circular economy, Citeo has set itself 5 commitments: to reduce the environmental impact of its customers' products by anchoring the circular economy and eco-design in their practices and strategies; to create the conditions for building the solutions of today and tomorrow that combine environmental and economic performance; to provide consumers with the keys to reducing the environmental impact of their consumption; to co-construct and promote the company's solutions and positions, from local to international scale; to cultivate the commitment of its employees in the service of its mission. Since the creation of Citeo, consumer goods and retail companies have invested more than 13 billion euros to develop eco-design, install and finance selective collection and create recycling channels, with their partners in local authorities, channels and operators. Today, 72% of household packaging and 62% of paper are recycled, thanks to the sorting gesture of the French, which has become the first eco-citizen gesture.
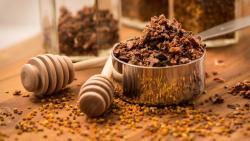
Since 1955, the Barbier Group has established itself as a major player in the flexible packaging sector. Our main industrial process is the extrusion of plastic films using "bubble" or "cast" technology. The Barbier Group is N°1 in France for polyethylene conversion and N°5 in Europe. The company is an independent, family-owned group. In 2022, the Barbier Group generated sales of €373 million, 35% of which were exported, and employs over 700 people. Over 170,000 tonnes of polymers (polyethylene and compostable co-polyester) were processed in 2022. Our finished products are destined for 3 markets: Industry (packaging and grouping films), Agriculture (films for livestock and market gardening) and the Bag Industry (garbage can liners, biodegradable bags for fruit and vegetables).
The Barbier Group has always pursued a proactive, innovation-oriented policy (the research and development budget represents over 2% of sales every year).
Our production units, spread over several sites (all concentrated in the Haute-Loire region), are among the most modern in Europe. Our policy of regular investment is geared to the constant expansion and modernization of our production capacities, the reduction of our environmental impact (reduction in thickness, increasing integration of recycled raw materials) and the upgrading of our products in order to pursue our development by offering our customers solutions adapted to their changing needs. The constant acceleration and increasing diversification of the integration of recycled raw materials in our products is a major challenge for the BARBIER Group.
By 2022, we will have integrated, on average, over 25% of recycled raw materials into our finished products. Our recycling activity is fully integrated. Our first recycling unit was set up in the early 1980s and was joined in 2015 by a second unit. We recycle post-consumer films of industrial and household origin, as well as agricultural films collected after use. The raw material recycled in our units is then used directly in our extrusion units. This integration is a major asset, enabling us to react quickly and adapt to changing circumstances.
With the increasing use of recycled raw materials in increasingly technical and diverse applications, the SUPER PE project fits perfectly into the Barbier Group's ongoing quest for innovation.

We invent and manufacture responsible packaging - tubes, lipsticks, mascaras, perfume covers, jars and turnkey solutions - for the beauty, skincare and health markets.
We believe there can be no responsible packaging without responsible business. That's why we uphold the reputation of our dynamic and prestigious customers; take action for the environment; support our communities; invest in technical expertise and world-class equipment for our 35 plants worldwide; and look after our 13,000 talented employees.
At Albéa, we protect Beauty.

The CTCPA (Centre Technique de la Conservation des Produits Agricoles) is a technical research and service center that has been assisting food companies for over 70 years with product and process development, food quality and safety, environmental and industrial performance, and packaging. The CTCPA provides services for all IAAs (from start-ups to large groups) in the form of audits-consultancy-studies, laboratory analyses (microbiology/molecular biology, nutritional quality, packaging), trials and pre-production runs in technology halls, process evaluations and intra- and inter-company training courses.
Historically, the CTCPA has provided collective research and technical[1]regulatory support for the canned, dehydrated and frozen vegetable industries.
More info : www.ctcpa.org and on social networks

Innovation Fluides Supercritique (IFS) is a center of expertise in supercritical and subcritical fluids, combining a network of academic and industrial players with an R&D center. Founded in 2006, IFS has become the French scientific and technical reference for the development of technologies using supercritical fluids. Thanks to a multidisciplinary scientific team and adapted supercritical equipment (from a few grams to several kilograms), IFS is able to respond to a wide range of supercritical fluid processes: extraction, purification, cleaning, impregnation and material testing.
IFS provides R&D services for companies and laboratories in the field of supercritical processes: monitoring, proof of concept, feasibility and optimization studies, engineering, technical and economic studies, training.
More info : www.portail-fluides-supercritiques.com and on social networks
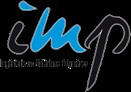
The laboratory Polymer Materials Engineering (IMP, UMR CNRS 5223) is a joint research unit between CNRS and three higher education and research establishments: INSA Lyon, Université Claude Bernard Lyon 1 and Université Jean Monnet Saint-Etienne. The IMP laboratory employs nearly 200 people, including 83 permanent staff and more than 110 doctoral and post-doctoral students. The Laboratory offers a unique set of skills covering the entire value chain in the field of polymer materials. IMP's strength lies in its ability to coordinate scientific knowledge and resources in order to implement an approach that is as effective as possible. multi-scale, multi-disciplinary engineering by assembling the fundamental building blocks of polymer chemistry and physics involved in laboratory and pilot-scale processes to design controlled-architecture polymer materials that are both environmentally friendly and functional.

IPC is the Industrial Technical Center set up by the plastics industry to catalyze plastics and composite innovation in France. It assists manufacturers with studies, establishing protocols, feasibility and technology transfer. Its network of experts covers the whole country and works with French and European technological and scientific players, enabling it to respond to companies' needs in terms of R&D, innovation, technology transfer and skills, whatever the process used. IPC is developing major resources with 3 expertise platforms to meet the major challenges facing the profession: DIS30 for the circular economy, PRINTER for the industry of the future and 3D printing, and HYPROD² for high value-added products.
IPC has been awarded the Institut Carnot Ingénierie@Lyon label for excellence in partnership research.
More info : www.ct-ipc.com and on social networks
Financial and technical support :
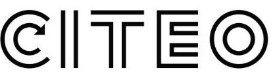