Packaging
Packaging reuse: a technical challenge for the entire value chain
23
Jan
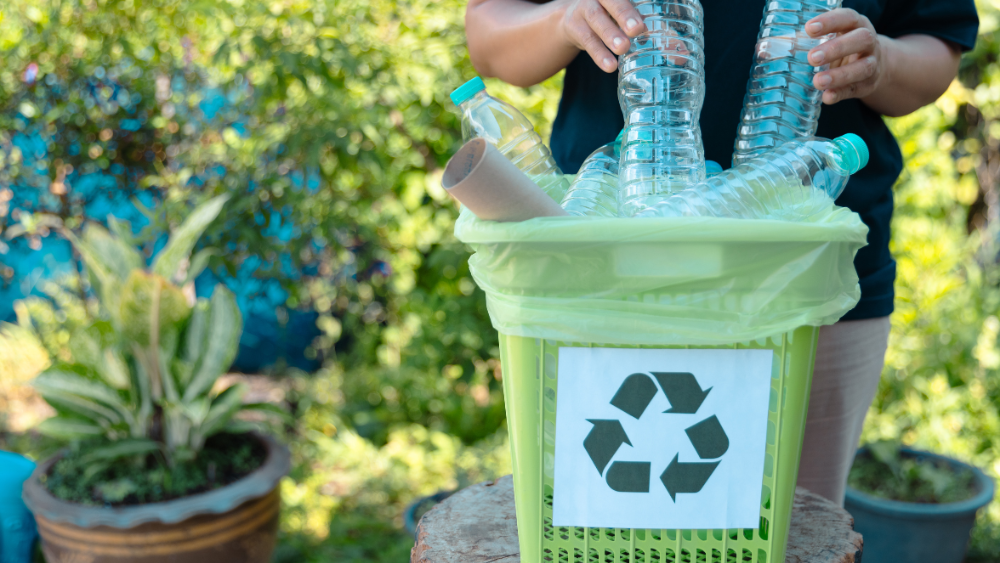
Published on : 23/01/2025
Introduction
Packaging reuse represents a major challenge for the entire value chain, from packaging manufacturers to washing companies, right through to the food industry. Beyond the simple question of washing, this model requires us to rethink the safety, quality and traceability of products at every stage of their life cycle. The reuse process raises new technical issues that must be anticipated to ensure the success of this transition. Discover in this article the issues, challenges and proposed solutions for mastering this change in the reusable packaging value chain.
To read the full article, download it here: TechTime Article - January 2025 - Reuse
Any questions? Contact Patrice DOLE, Research & Innovation Director: pdole@ctcpa.org